Fakuma 2023
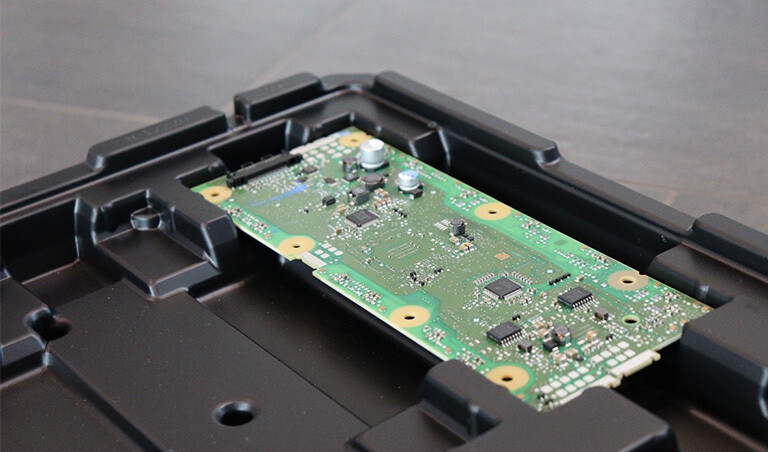
Increased flexibility. Reduced energy consumption. ILLIG presents innovative solutions for thermoformed technical parts
At Fakuma 2023, ILLIG – one of the world’s technology leaders for thermoforming machines – will be presenting a comprehensive portfolio of solutions and machines with a focus on the forming of technical plastic parts in hall A3, booth 3005. Under the motto “Performance for a sustainable future”, the Heilbronn-based company will present high-performance thermoforming systems with roll and sheet loading for the cost-efficient production of precise formed parts. ILLIG has a new machine in its portfolio in Friedrichshafen: the UAF, newly presented this year, with flexible clamping frames and integrated preheating and finish heating. Development here was focused on flexibility and reduced energy consumption.
“The main aim of our development work in this case was to improve the energy efficiency of the thermoforming systems and achieve the relevant reduction of CO2 in the manufacturing process,” explains Jürgen Lochner, CSO/CTO of ILLIG. “Due to the current overall economic situation, energy-efficient technologies are the market drivers and will remain so for a long time to come. Customers and anyone interested can obtain comprehensive information on site about the advantages of our latest sheet processing thermoforming machine UAF, and also on the topics of energy efficiency and automation,” Lochner continues.
The fields of application for the technical parts produced using the thermoforming process range from e-mobility or classic automotive and commercial vehicle applications, through to transport and logistics solutions, caravans, sanitary and household. Weight-optimised car body parts or battery covers can be formed cost-effectively from plastic, for example.
From the sheet: forming areas from 600 x 500 mm to 3,000 x 2,000 mm, drawing depths of up to 800 mm
ILLIG has two systems to meet different requirements in its portfolio: the UAF and UAg sheet processing thermoforming machines. The entirely newly developed sheet processing thermoforming machine UAF launched at the beginning of 2023 with its flexible clamping frames is the number-one choice when it comes to flexible production of small to medium batch sizes with frequent tool changes. Developed from scratch, the machine has an automatic sheet loading system and an integrated preheating and finish heating system that realises shorter cycle times and guarantees an optimum forming process. The UAF is available in four sizes for all standard sheet formats.
For this newly developed machine, special emphasis was placed on an energy-efficient design: servo motors, regenerative drives, preheating and an efficient heating system all add up to reduced energy consumption and therefore lower energy costs per formed part. A tool change on the UAF is possible in under 30 minutes. Forming tools made by market competitors can now be used, too. For post-processing, ILLIG offers various options and handling systems via partners. With the UAF, the system supplier with its own toolmaking unit continues to pursue its path towards higher performance, enhanced sustainability and increased flexibility.
ILLIG offers a proven sheet processing thermoforming system in the form of the UAg. ILLIG’s UAg has always stood for very short cycle times and maximum output, and it continues to set the benchmark here. Combining the UAg with fixed clamping frames enables the very highest final vacuum levels to be achieved. The final vacuum level is directly reflected in the sharpness of the formed part. The UAg series covers forming areas from 270 x 170 mm to 2,450 x 1,450 mm with drawing depths of up to 700 mm. This means it is particularly suitable for formed parts in large batch sizes. Automation via a sheet or roll loading unit is possible with all UAg machine types.
Most recently, ILLIG has worked with its customers to optimise the machine and process configuration of the UAg series in order to achieve maximum output. For example, considerably higher cycle times can be achieved by using a third heating station. With an investment of 25% of the total cost for this extension, it is possible to increase the performance of the machine by up to 90%. Tool changes on the UAg have been optimised, too. The so-called quick tool change can be carried out within 15 to 20 minutes with a package combining upper tool, clamping frame set and lower tool.
The UAg machines with fixed clamping frames can be configured to suit individual customer requirements. They offer a cost-efficient entry-level option as well as a wide range of upgrade options to create a high-end modular system. Here, too, ILLIG offers new possibilities with regard to energy consumption: for example, the main axes can be fitted with servo motors instead of pneumatic drives.
“We always offer our customers innovative and contemporary thermoforming systems by consistently optimising well-established solutions and aligning new developments based on specific customer and market requirements. The UAg and UAF series are good examples of how we’re increasing flexibility for our customers in the field of UA machines”, says Erik Hemgesberg, Vice President Business Unit Thermoforming and Packaging Systems.
Off the roll: plastic parts with forming areas ranging from 500 x 365 mm to 800 x 600 mm and drawing depths of 80 mm or 120 mm
With the RDF 85 and the RV series, ILLIG shows that technical formed parts such as transport trays can also be produced using classic thermoforming systems with roll loading. Roll processing enables initial thicknesses of the semi-finished products up to a maximum of 2.5 mm. The benefits here lie in low tool acquisition costs and high article output (forming pressure: 6 bar in the RDF 85, 1 to 3 bar in the RV machines).
With the RDF 85 from the ILLIG RedLine segment, formed parts for different requirements can be produced cost-effectively – to ILLIG’s customary standards in terms of quality and performance. Thanks to an open tool interface, tools from the customer’s inventory or made by market competitors can now also be used for the first time. The modular machine tool kit offers even greater flexibility in the creation of formed parts.
Technical parts made of thermoformed plastic offer wide-ranging benefits
The thermoforming process offers significant benefits both in terms of the production process and the formed parts themselves: cost-efficient parts production can be set up with a comparatively low investment, with short creation and change cycles, and also low energy requirements compared to other production processes. One significant advantage of formed parts made of thermoformed plastic such as car body or interior trim parts is their low weight – a factor that is crucial both in vehicle construction and in transport logistics. Taking into account the robustness and durability of plastic parts, such as (reusable) transport pallets, their sustainability footprint can be better over the life cycle compared to conventional solutions such as wooden pallets. In addition, plastic transport solutions offer a high level of transport or product protection, thereby contributing to the sustainable handling of high-quality products. For transport trays used in the production of electronic components, for example, the issues of ESD protection and precise product loading are likewise key factors. Automotive formed parts do not need to be additionally painted and are UV-resistant.
Increasing focus on energy consumption and CO2 reduction
ILLIG firmly believes that energy-efficient thermoforming systems not only promote the customers’ business success but also reduce the impact of the manufacturing process on the environment. Energy consumption and the CO2 reduction are key decision-making criteria and competitive factors. In addition to economical production systems, ILLIG also offers its customers support in the form of calculations that can be included in applications for subsidies, for example. At the Fakuma exhibition booth A3-3005, the ILLIG team of experts will be more than happy to provide customers and anyone interested with individual information on this and on the upgrade options for existing systems.
Images
01. ILLIG sheet processing thermoforming machine UAF (front view)
02. ILLIG sheet processing thermoforming machine UAF (side view)
03. Thermoforming system with roll loading, RDF 85 RedLine (front view)
04. Thermoforming system with roll loading, RDF 85 RedLine (side view)
05. Thermoformed reusable packaging for enclosure shells
06. Thermoformed transport solution for electronic components
07. Thermoformed transport trays for printed circuit boards
Download
Press kit
Downloads
About ILLIG
ILLIG is a leading global supplier of thermoforming and packaging systems as well as tool systems for cardboard,
paper and plastics. The company's product and services portfolio includes the development, design, manufacture,
installation and commissioning of complex production lines and components. With its unique approach to packaging
development, “Pactivity® 360”, ILLIG supplies its customers with resource-friendly and sustainable solutions.
With its subsidiaries and sales agencies, ILLIG is active in all markets around the world.
More than 75 years, the family business has been serving its customers as a reliable partner for the cost-effective
manufacturing of complex precision packaging and parts with innovative technology of unsurpassed quality
and comprehensive global service.
Further information:
Marketing & Communications
Tel.: +49 7131 505-236
E-Mail: Media@illig.com
Note: Terms marked with ® are registered and protected trademarks of
ILLIG Maschinenbau GmbH & Co. KG. Pictures: ILLIG